Kuraray’s Approach to Safety
For the Kuraray Group’s business activities, safety is an absolute necessity, and the cornerstone of everything we do. Building “Trustful workplaces, and a safe and accident-free company” is a key theme required for maintaining stable product supply and trustworthiness for society.
With these concepts in mind, the Kuraray Group has established and implemented a safety management system to undertake various activities. A number of initiatives are promoted to raise the safety awareness of our employees and have safety behaviors and confirmation established as a common practice at work.
Each worksite discovers process safety risks and occupational risks through risk assessment activities, and prevents the occurrence by promoting inherent safe measures for facilities. In preparation for accidents or disasters, we make efforts to minimize damage and prevent the recurrence of accidents or disasters, such as by holding emergency drills or sharing information on accidents or lessons.
- Guiding Principle on Ensuring Safety
- Safety is the
cornerstone of
everything we do
- Action Courses on Ensuring Safety (FY2018)
- Ensuring “Safety First, Production (Construction and R&D) Second”
- Take a Breath and Check before every Action, in order to eliminate unsafe situation (action, behavior, or condition)
- Take action toward Zero Occupational Injuries and Zero Process Accidents as the Responsibility of Each Employee
Safety Activity Management
In accordance with the Company's Safety Activity Management Regulations, the Kuraray Group develops a safety plan every fiscal year and implements it to ensure occupational safety, process safety, and disaster prevention. To be more specific, at the Safety Promotion Committee attended by the President and executives in charge, we make an overall assessment and have a discussion on safety activity performances of the current fiscal year and establish an activity policy for the coming fiscal year. This policy is reflected in and implemented through specific action plans of each plant and department. A group of safety representatives from the headquarters, including the executives in charge, visit every plant in Japan twice a year to examine their activity plans, progress management, and the results.
The domestic Kuraray Group focuses on activities for further enhancement of process safety level by implementing risk assessment of unusual tasks and situations including a total power blackout and emergency stop to discover and address potential risks. In addition, we conduct activities to systematically take over operation techniques and technologies from experienced operators to non-experienced operators. In the future, through the evaluation by external organization on the safety system and corporate culture, the Group will discover points to be strengthened further and aim to create process accident-free and occupational incident-free, safe workplaces by rotating the PDCA cycle.
As for the overseas affiliates, the global foundations of safety activity, including a system to share information related to an accident/incident that has occurred and its countermeasures, has been constructed. Global meetings of the environment and industrial safety division and global deployment of a management system for safety activities have been organized to be started in 2018. Kuraray will undertake these activities aiming to improve the level of group-wide safety in the future.
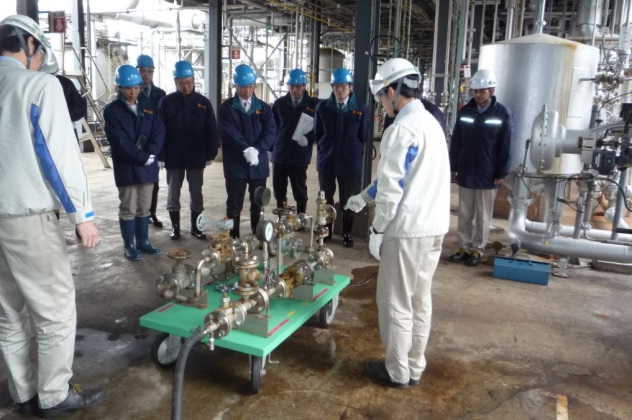
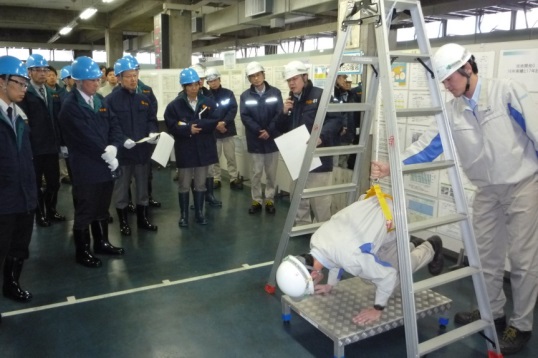
Targets and Performance in Safety Priority Activities
Evaluation: Ο Accomplished, Δ Nearly accomplished, Χ Not accomplished
FY2017 | FY2018 Priority Activities | |||
Target | Performance | Evaluation | ||
Process safety and disaster prevention Occupational safety |
Enhancement of safety awareness of individual persons (Prevention of accidental dangerous behavior at the moment) |
Safety awareness was improved by activating characteristic activities such as review after work, teaching with questioning, and interaction between departments. | ○ |
|
---|---|---|---|---|
Implementation of risk assessment of unusual work | Progress was made further toward the identification of risks and the consideration of countermeasures in case the situation that does not progress as expected, or in case of power outages and emergency stops, and so on. | ○ | ||
Implementation of inherently safe countermeasures for serious risks, or minimizing damage | Unique initiatives of each department made progress, as did inherently safe countermeasures for serious risks or minimizing damage. | ○ | ||
Capability of detecting abnormal signs and dealing with abnormal situations(Improvement of technical skills through accumulating experience) | Improvement of response skills was achieved by improving training assuming holiday night, equipment failure, and absence of the leader from the workplace and so on. In addition to clarifying criteria for judging abnormalities, we worked on education to raise sensitivities to danger and improved the ability to detect abnormal signs. | ○ | ||
Constructing a base for globalization of safety activity management | Starting full-scale operation of the labor accident assessment system and awarding criteria commonly used both in Japan and overseas, we promoted the sharing of accident information and so on, and facilitated the Company’s infrastructure to bolster management on a global basis. | ○ |
Numerical Target and Performance
FY2017 | FY2018 | |||||
Target | Criteria for evaluation | Actual | Target | Criteria for evaluation | ||
Process safety and disaster prevention | Japan | Zero | Process accident: 1 or less | 3 | Zero | Process accident: Zero |
---|---|---|---|---|---|---|
Outside Japan | - | 2 | Process accident: Zero | |||
Occupational safety |
Japan | Zero | AB rank accident: 2 or less*1 | 1 | Zero | AB rank accident: Zero |
Outside Japan | - | 0 | AB rank accident: Zero | |||
Japan | Frequency rate of all occupational incidents: 0.8 or less*2 | 0.95 | Frequency rate of all occupational incidents: 0.5 or less*2 | |||
Outside Japan | - | 5.27 | Frequency rate of all occupational incidents: 3.0 or less*2 |
*1 Rank A and B: An evaluation ranking of occupational incidents using Kuraray’s proprietary system that rates the seriousness of occupational incidents from A to D in accordance with the levels of potential disorders and with the levels of faults that caused such incidents. An incident rated A or B is considered to be a serious incident.
*2 The frequency rate of all occupational incidents: The number of all occupational incidents requiring medical attention per million working hours.
Process Safety and Disaster Prevention
At the Kuraray Group, we consider it our major responsibility to prevent the occurrence of explosions or fires, leakage of hazardous materials and other accidents that could have an immense impact on society, as well as to minimize any damage in the event of such occurrence. For this purpose, we have continuously undertaken activities such as risk assessment related to process safety and disaster prevention, and strive to take earthquake and tsunami countermeasures for buildings and plants, and organize the safety management system for facilities.
After a recent accident occurred at another company, we paid particular attention to the risk assessment of unusual tasks and situations such as the starting and ceasing of an operation, a power and water outage and an emergency shut-down. Moreover, we extract various risks that may arise in the event of a failure of safety equipment or incompliance with a rule, and consider countermeasures thereto.
Additionally, we develop ideas and human resources that can promptly respond to an unusual situation before an accident occurs through implementing education to raise the members’ sensitivity to risks and clarify standards to determine an unusual situation, so that they can detect a sign of abnormalities.
Employees are regularly trained through on-site drills on various situations including the night time, holidays, when managerial personnel are absent and situations that occur without notice, in a drill using an external facility or a joint drill with a local fire department.
In the event of a significant accident, the Emergency Command Center led by the Representative Director is ready to be established to promptly respond to the situation and provide on-site support. In fiscal 2017, a company-wide drill involving the Emergency Command Center was held on the assumption that a fire breaks out at a plant in the absence of the Representative Director and the Emergency Command Center advises neighborhood residents to shelter. Media training is also provided to key managerial personnel in charge of public relations to enable them to appropriately provide information to the regional community and media in case of such an accident.
In fiscal 2017, we regret we had five accidents at whole Kuraray Group including one indoor oil leakage and two cases of CFC leakage from air conditioners in Japan, and one minor explosion of equipment undergoing maintenance and one fire occurred at a waste container abroad.
Occupational Safety
Realizing that the safety and health of its employees are the basis of business activities, the Kuraray Group aims to create safe and accident free workplaces by striving to enhance the safety level of each of its employees and organizations. It does this through appropriately implementing its occupational safety management system. Through the Company-wide policies and activity items including Guiding Principles and Action Courses on Ensuring Safety, policies and plans are developed and put into practice according to each plant’s and division’s situations and their unique ideas. Safety activities and their challenges are discussed among workers and employers at the Safety and Health Committee held by each of the domestic plants and factories every month, aiming to realize “trustful workplaces, and a safe and accident-free company."
Through risk assessment activities and intrinsically safety measures of equipment, activities to reduce equipment-caused accidents have successfully reduced serious occupational incidents. However, many occupational incidents caused by an individual’s carelessness and unconscious behavior still occur. Therefore, education to raise the members’ sensitivity to risks is promoted to eliminate these types of occupational incidents.
In fiscal 2017, the frequency rate of all occupational incidents of the Kuraray Group in Japan was 0.95 and that of overseas affiliates was 5.27.
For an appropriate analysis of occupational incidents, the Kuraray Group in Japan rates them using the Group’s proprietary indicator. Starting from fiscal 2017, the indicator has also been applied to those of overseas affiliates, enabling an assessment of occupational incidents at whole Kuraray Group based on a common indicator. From fiscal 2018, the indicator has been used as an assessment standard of a safety target.
Evaluation and Classification of Occupational Incidents
Generally, categories based on the severity of actual incidents, including fatal incidents, lost time incidents and non-lost time incidents, are used as an indicator for occupational incidents. In particular, the frequency rate of lost time incidents is often used to assess the level of or establish a target for organizational safety.
However, actual safety levels may deviate from the results of this assessment method for the following reasons:
- (1) The severity of injuries is unpredictable in many cases.
- (2) The occurrence factors of an accident are not taken into consideration.
- (3) (When it is applied to global management) criteria of determining the degree of injuries depends on the country.
We therefore have established a proprietary evaluation and classification of occupational incidents by subtracting unpredictable factors and adding an assessment of occurrence factors. This quantifies not the actual severity of injuries but the potential severity of injuries that could have been caused by an occupational incident. Moreover, faults that caused such incidents are divided into human, equipment and managerial, rated numerically, and added to the potential severity of injury to determine the ranking from A, B, C to D.
As a result, the number of severe occupational incidents ranked A and B serves as an indicator for evaluating the level of organizational safety.
Focus: “Experience-based Safety Class” Using Hazard Experience Training
To raise the sensitivity of risks of employees who have little experience of incidents and irregularities at production sites, experience-based education that could raise the members’ sensitivity to and knowledge of risks on site is effective. In 2015, the Kuraray Group introduced a facility which provides a real hazard experience in the Okayama Plant to hold an experience-based safety class.
In the class, participants can experience a hazardous incident such as getting caught in a roller, being hung by a safety belt, or having their cuffs caught in a rotating body, while being aware of something that cannot be gained through books and discussions.
The domestic Kuraray Group, in 2017, started the “Experience-based Safety Class” at the Saijo Plant following the Okayama Plant, and is also preparing to introduce it at the Kurashiki Plant. Training sessions are also held by external professionals of hazard experience at our plants or an external facility.
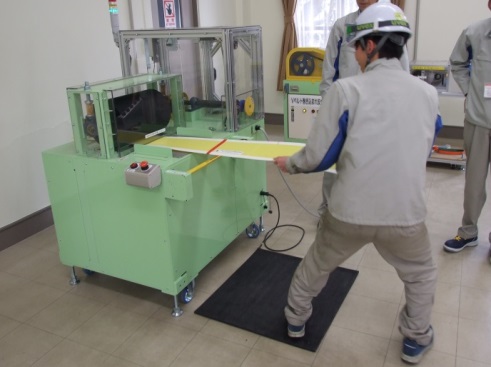
Logistics Safety
To prevent damage to society at large caused by logistics accidents, the Kuraray Group is engaged in an ongoing promotion of activities to ensure logistics safety from the aspects of product shipment and storage.
The Kuraray Logistics Safety Conference, which is the core organization for this activity, marked its 17th year. In fiscal 2017, a symposium on “Safety Control at Production Site” was held having a Specially Appointed University Professor as a speaker. Hazardous material acceptance work was verified on site at the Niigata Plant, and measures to prevent significant accidents were shared among participant companies (10 hazardous materials transportation contractors), to raise their awareness of logistics safety.