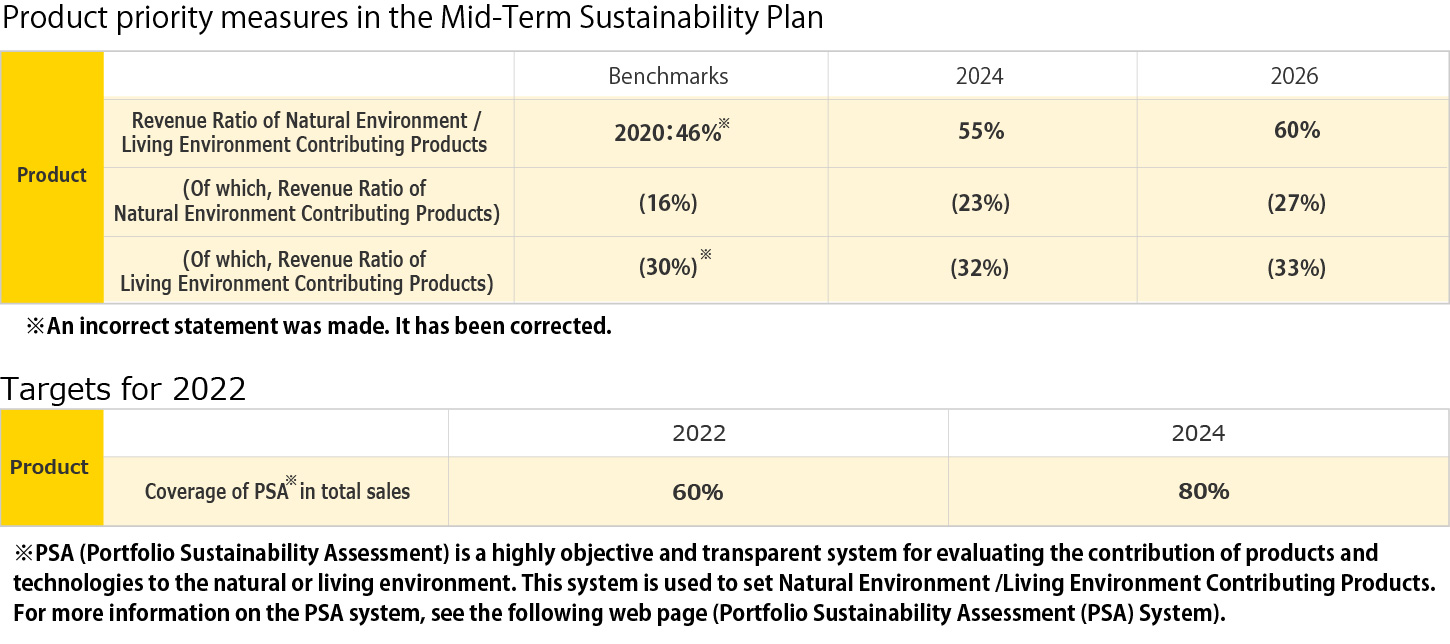
Quality Management
Kuraray’s Approach to Quality
The Kuraray Group’s approach to quality is rooted in the realization of the Kuraray Group’s Mission: “For people and the planet—to achieve what no one else can.” Our products and services can only be valuable when the values are recognized and accepted by customers. In other words, we have made it clear that Kuraray’s concept of quality is “customer satisfaction.” In order to provide products and services that achieve customer satisfaction and contribute to society, we believe that it essential not only to pursue the performance and quality of our products and services but also to consider multiple aspects, including safety, environmental impact, and sustainability.
For this reason, it is necessary to conduct comprehensive quality management in both manufacturing, such as production and development, and in sales, distribution, storage, value chains and so on, and we are promoting initiatives with the participation of all employees.
Quality Management
The Kuraray Group clearly states that the officer in charge of the Corporate Sustainability Division supervises quality assurance for the Group in its internal rules for quality assurance and product safety.
While respective business divisions, which know their products well, take responsibility for quality assurance and product safety, the Corporate Sustainability Division as a corporate function systematizes quality management at respective business divisions with a view to ensuring continuous improvement. It is also in charge of conducting quality audits for respective business divisions from an objective viewpoint to confirm the reasonableness of quality assurance operations.
Respective business divisions and the Corporate Sustainability Division have regular meetings regarding quality to share information and work together to ensure and improve quality.
The Kuraray Group sets out that “we will constantly develop and provide safe, high-quality products and services” in our Corporate Statements, and have formulated the Kuraray Group Global Quality Policy to make our corporate stance toward quality clearer.
Kuraray Group Global Quality Policy
“We contribute to the society by supplying safe, reliable and high-quality products and services.”
We vow to provide safe high-quality products and services with a sense of responsibility and pride, and contribute to improved natural environments and living environments with a view to realizing a sustainable society.
To that end, each one of us will engage in improvement activities continuously to pursue the creation of value to enhance customer satisfactions with better understandings of demands of laws and regulations, society as well as needs of customers.
We also set “annual action plans” regarding points that should be focused on to improve awareness toward quality in the employees of the Kuraray Group and provide products that offer greater satisfaction to customers.
We ensure correct operations to support implementation of the Kuraray Group Global Quality Policy. We have established the Kuraray Group Product Safety Regulations, which clarify requirements for product liability, chemical substance management, and quality management, as well as various subsets of internal rules and detailed regulations.
Quality Assurance Activity
Quality assurance activities of the Kuraray Group include 1) systematized activities with ISO as a basis, 2) those carried out by respective business divisions and departments on their own (flexibly), and 3) those carried out jointly by the Corporate Sustainability Division and respective business divisions.
With regards to ISO 9001, which serves as a foundational structure for our Quality Management System (QMS), certifications are primarily obtained by each production site, which develops a framework for quality assurance based on ISO9001 and carries out quality management and quality assurance activities on a daily basis.
We have also obtained certifications for ISO13485 (QMS standard for medical devices), IATF16949 (QMS standard for the automobile industry), and others, depending on our businesses.
With respect to IATF 16949, the Advanced Interlayer Solutions Division was certified a long time ago and the EVAL Division has worked on being certified globally. EVAL Europe N.V. obtained certification in 2018 (transition from ISO/TS16949 obtained in 2003), while the EVAL Business Unit of Kuraray America, Inc. and the EVAL Division in Japan (Okayama Plant) completed the certification process in 2019, and we are continuing our quality improvement activities.
Quality improvement activities carried out by each business division or department include soushin katsudo (innovation activities) conducted by each division at each production base. Good practices for quality improvement activities are shared through in-house reporting meetings, quality conferences, and quality reporting meetings at internal companies and divisions.
In addition to these activities undertaken by each business division or each department, we have initiatives in place that aim to upgrade quality management for the entire Group with the collaboration of the Corporate Sustainability Division and respective business divisions. From fiscal 2020, we have begun considering the introduction of a quality control system (digital storage of data, direct storage from analytical equipment, and linkage with a backbone system) to standardize the quality control workflow and prevent human errors such as typographical errors. We are moving forward with preparations for some departments to pilot the adoption of this system ahead of the rest of the organization.
Going forward, we believe that it will become increasingly important to ensure the maintenance and administration of comprehensive quality management spanning distribution and storage, not only manufacturing such as production and development, and we will work on this as a priority issue to further enhance the reliability of our product and service quality for customers through the participation of all employees involved in business activities.
Quality Assurance Education
In fiscal 2016, the Kuraray Group compiled the Group’s views on quality and issued the Kuraray Group Quality Handbook for employees. This Quality Handbook prescribes the following five basic key items commonly applied to all members working for the Kuraray Group:
1 | That everyone participates in striving for quality (participation by everyone) |
---|---|
2 | That everyone bases their conduct on facts (fact-based management) |
3 | That employee conduct conforms to the “5G principle” of genba (actual place), genbutsu (actual products), genjitsu (actual facts), genri (theory), and gensoku (fundamental). |
4 | That employees satisfy the requirements for a given process before going on to the next process (building quality into processes) |
5 | That employees constantly strive to improve quality (continuous improvements) |
Together with the distribution of this quality handbook, employees receive basic education on the quality handbook in an e-learning format. Through this type of basic education, we are committed to anchor awareness in employees that each of them plays an important role in customer satisfaction. We will continue to have everyone in the Kuraray Group work on daily operations to realize “customer satisfaction” rooted in those five important items.
At the same time, as a more practical type of education, we are focusing on in-house seminars aimed at raising the level of managers in charge and staff in quality assurance. In fiscal 2021, from the perspective of how to approach quality improvement activities, we held an in-house seminar in which an outside presenter spoke about the theme of “Preventing Recurrence with Certainty using Why-Why Analysis.” The seminar was attended by employees from production, sales, and development departments as well as to quality assurance and quality control. In addition, we also held a seminar for heads of departments in fiscal 2021, enabling group discussions among heads of quality control, production, and sales departments on specifications and quality standards. We are attempting to improve communication within and between departments by encouraging discussions across business sites and divisions.
Actions to Be Taken in Case of a Product Accident
Within the Kuraray Group, information on complaints and claims received from customers is managed by its divisions, so responses to customers can be made promptly and action taken swiftly to prevent recurrence of the same flaws. However, Group-wide response schemes for material complaints and claims are prescribed by the Rules-on Product Liability-related Accident Response and Quality Complaint Report.
On the occurrence of a material product accident, the Corporate Sustainability Division will submit a situation report to the management and an administrative agency set forth by law, while establishing the Corporate Emergency Headquarters to take prompt and appropriate action from the customer’s point of view. Moreover, a mechanism to take corrective actions to clarify the cause and prevent recurrence has been established not only for a material product accident which requires an emergency arrangement but also general accidents.
In fiscal 2021, no product recalls or accidents that cause severe damage to health or damage to property such as fire were reported within the Kuraray Group.
Quality management system certifications (as of the end of December 2021)
- (1) ISO9001
-
- Kuraray Niigata Plant
- Kuraray Kashima Plant
- Kuraray Okayama Plant
- Kuraray Kurashiki Plant, Membrane and Module Production Technology Development Department
- Kuraray Kurashiki Plant, Film Production and Technology Development Department
- Kuraray Kurashiki Plant, Research and Development Division, Functional Products Development Department
- Kuraray Tamashima Co., Ltd. (Ester Plant)
- Kuraray Saijo Plant
- Kuraray Tsurumi Plant
- Kuraray Plastic Co., Ltd. (Ibuki Plant)
- Kuraray Fastening Co., Ltd. (Maruoka Plant)
- Kuraray Engineering Co., Ltd.
- Kuraray Trading Co., Ltd. (Okayama Plant)
- Kuraray Techno Co., Ltd. (Building Management Service Division)
- EVAL Europe NV
- Kuraray Europe GmbH
- Kuraray Europe GmbH Business Area PVB
- Kuraray America,Inc. EVAL BU
- Kuraray America,Inc. Septon BU
- Kuraray America,Inc. PVA Division
- Kuraray America,Inc. PVB Division
- Kuraray America, Inc. Vectran Division
- Kuraray America, Inc. Trading BU
- Kuraray Korea Ltd.
- Kuraray Europe Moravia s.r.o.
- Kuraray Asia Pacific Pte.Ltd.
- MonoSol, LLC
- MonoSol AF, Limited
- Plantic Technologies Limited
- Calgon Carbon Corp
- Calgon Carbon Suzhou
- Chemviron S.A. Feluy & Chemviron Carbon Ltd Tipton
- Chemviron Carbon Limited Ashton -in-Makerfield
- Chemviron Italia SRL
- Chemviron France SAS
- Chemviron Carbon Cloth Division a Division of Chemviron Carbon Ltd.
* This includes the following group companies which reside within business sites and plants:
Kuraray Saijo Co., Ltd., Kuraray Kuraflex Co., Ltd. (Okayama Plant), Kuraray Okayama Spinning Co., Ltd., Kuraray Techno Co., Ltd.
- (2) ISO13485
-
- Kuraray Noritake Dental Inc.
- Kuraray Functional Materials Company, Medical Division, Biomaterial Department
- Kuraray Europe Benelux B.V.
- Kuraray America, Inc. Vectran Division
- Chemviron Carbon Cloth Division a Division of Chemviron Carbon Ltd.
- (3) IATF16949
-
- EVAL Europe NV
- Kuraray America Inc.-EVAL BU
- Okayama Plant, EVAL Division
- Kuraray Europe GmbH Division Troisdorf
- OOO TROSIFOL
- Kuraray Korea Ltd.